Making the green tire even greener
Essen, Germany – Michael Kempf, Head of Market Segment Tires & MRG at Evonik’s Silanes Business Line, outlines how the coupling agent XP Si 466 EXT boosts the sustainability of passenger car tires.
Q:
Mr. Kempf, in the Paris Climate Agreement, the world pledged to reduce CO2 emissions to mitigate global warming well below 2 °C. How can the tire industry contribute to this goal?
A:
For the tire industry, a more sustainable and environmentally friendly production is more important than ever before. The Silica/Silane system in tires contributes to reducing fuel consumption and CO2 emissions by reducing rolling resistance. Minimizing emissions during the entire lifecycle of a product is key to achieving the goals of the Paris Agreement. True to Evonik’s aim of Leading Beyond Chemistry, we strive to be an enabler, bringing sustainable solutions to our customers, and a role model, leading by example in our own operations.
Q:
Which sustainability benefits do rubber silanes offer to the tire industry?
A:
Since the introduction of the Silica/Silane-system, Evonik has continued to address the challenges facing the industry and advanced the technology behind tires. For example, during tire production, often volatile organic compounds are emitted. Our silane XP Si 466 EXT, eliminates the release of any volatile organic compounds during processing, boosting the sustainability of the tire industry.
Q:
How does the Silica/Silane-system work?
A:
The Silica/Silane-system is all about improving the performance of rolling resistance and wet grip without compromising on abrasion resistance. These three key aspects are known as the magic triangle. In tires it is well known that silica and rubber do not mix. An additional component is required to bond polar silica and non-polar rubber. In the 1990s, researchers discovered that organosilanes are an outstanding bonding material between silica and rubber, and the Silica/Silane-system was introduced.
Rubber silanes consist of three structural units: the silica-reactive unit, the organic spacer, and the polymer-reactive unit. During mixing, the silica-reactive unit reacts with the silanol group of the filler and during vulcanization, the polymer-reactive unit reacts with rubber. The silica-reactive unit is often an ethoxy group, which emits ethanol on formation of a covalent bond with silica. With XP Si 466 EXT, the release of volatile organic is avoided.
Q:
What is so special about this silane?
A:
XP Si 466 EXT is a bifunctional molecule, in which all alkoxy groups are replaced by a non-volatile leaving group. Therefore, no volatile organic compounds are emitted during mixing and vulcanization. It’s performance in tire compounds was tested against a standard Green Tire and it was matched. In the key performance areas—wet grip, rolling resistance, and abrasion resistance—were all comparable. With this coupling agent we’re making the Green Tire even greener.
Q:
If you say the performance is on a comparable level – what does that mean exactly?
A:
The reduced rolling resistance really makes a difference. We know that Green Tires featuring the Silica/Silane-system can cut fuel consumption by up to 8 %. What’s more, an improved wet grip means that braking distance is significantly reduced. Drivers do not only see an impact on their wallets, but their safety is improved too. Generally, tires based on XP Si 466 EXT are more sustainable and any savings made in fuel consumption, reduce the carbon footprint of the tire.
Q:
How are these performance improvements perceived by the markets?
A:
The performance difference between conventional and Green Tires has been highlighted by regulators. Since 2012, the EU tire label has provided more transparency for drivers. Tires are classified from A (best) to E (worst) based on the tire’s rolling resistance, wet grip, and noise levels. The efforts to increase transparency through labeling is spreading to other regions of the world as well. In Europe, the Silica/Silane-system in car tires already has become the norm. However, stricter regulations and an increasing consumer desire for more sustainability is driving the demand for sustainable solutions in the tire industry. From 2010 to 2015, the market share of Green Tires in total sales volume increased from 10 % to 30 % globally.
Q:
Mr. Kempf, you stated earlier, that Evonik Silanes aims at being a paragon for sustainability, leading by example in its own operations. What do you mean with that?
A:
Acting responsibly and creating value for society is key to success. I am convinced by that. Chemistry plays an integral role in solving our world’s sustainability challenges. At Evonik, we strive to be an example in our own sustainable business operations and practices. In the Silanes business line, we address sustainable operation in different ways. For example, we mostly use bioethanol and regional suppliers to reduce the carbon footprint of our products. At our production site in Rheinfelden, Germany, we produce functional and chlorosilanes. Production at this site is mainly powered by hydropower so the majority of its energy consumption is virtually carbon neutral. Or take our site in Antwerp, Belgium. Materials are produced in an integrated structure. Starting with silicon metal, all essential raw materials are produced in one place, which avoids the transport of intermediates. The site is a pioneer within Evonik with regards to alternative energy. Back in 2013, we installed the first wind turbine at a chemical site at this site. Up to today, we use the energy it produces in the production processes.
Q:
Can you share some more concrete goals for the future with us?
A:
Evonik on a group level is working on reducing its raw material backpack by 15 % by 2025 compared to 2020. Basically, we want to reduce Scope 3 emissions in the upward value chain. To do so, we partner with suppliers and customers that pursue stringent sustainability policies.
Q:
What is the key to more sustainability?
A:
Innovation—it was key 50 years ago and it will be key in the next 50 years. Constantly focusing on innovation and the future, while maintaining availability and reliability, has meant Evonik can continue serving its customers with innovative and quality products. Materials with continued outstanding performances are only possible if innovation is a key part of the business model.
Q:
But Green Tires were originally developed in the 1990’s…
A:
That’s true. In the 1990s, researchers at Evonik realized that organosilanes act as an outstanding linker between silica and rubber. With that the Silica/Silane-system was introduced. But if you dig deeper, the story goes back even further. For me, Si 69® was the product that kicked off the change—a product first developed by Evonik researchers in the early 1970s. This polysulfidic bifunctional silane is well known in the industry and has been a standard component in car tire treads for a long time.
The success story of the Green Tire in the 1990s was built on Si 69®. 50 years after it entered the market, it remains an innovative product. And today, the same innovation and reliability continues with XP Si 466.
Q:
If innovation paves the way to more sustainability. What is the key aspect to focus on? Increased performance?
A:
We have consistently provided the products our customers need to overcome the challenges they face. From developing Si 69® in the 1970s, the Green Tire in the 1990s, to now, Evonik continues to stay ahead of the curve by investing in technology.
Our researchers do not only focus on performance, they extensively test with regards to the processability and production of tires. We don’t see car tires as another rubber product—they are high-tech composite materials, which require constant innovation to ensure reliability and performance. We focus on every aspect of the tire.
Q:
How do you ensure that your silanes for these high-tech composite materials meet customer’s demand?
A:
I love talking about this because it is something that makes me really proud. We have been the innovation partner of choice for tire manufacturers, and consistent performance is key. We work hard every day to maintain our position. Our deep understanding of silane chemistry puts us in pole position to help manufacturers worldwide innovate. At the same time, this close cooperation ensures that the focus is on the industry’s most pressing topics. Research and development capabilities are followed up with technical services to ensure superior and constant product quality. Investment in testing for performance and processing is continually occurring so our products are tested to the highest standards.
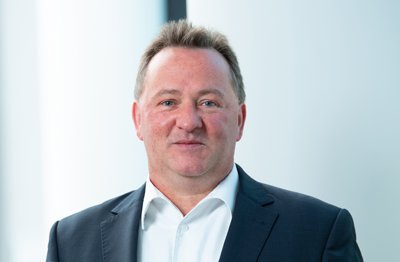
Q:
In all honesty, isn’t innovation only half the job? After all, you must make sure that innovations are really put in use…
A:
You have hit the nail right on the head! And this is where our global presence really kicks in: we have local proximity. Evonik is a global player. Our magic triangle is innovation, availability, and reliability and there is no compromise. With production sites for rubber across three continents and further technical sites spread across the globe, we are in a unique position to guarantee local availability and technical support.
Michael Kempf is the Head of Market Segment Tires & MRG at Evonik’s Silanes business line since June 2019. He joined Evonik in 1995. Before assuming the global marketing responsibility for Tires & MRG Michael held different positions within Evonik’s Silica business line and worked for several years as an expatriate for Evonik China in Shanghai, P.R. China. He graduated as Chemical Engineer and is certified as Marketer by the Business School of the University of Mannheim, Germany.